It is the legal and moral responsibility of any employer, to demonstrate that they have exercised due diligence in the design, build, install, test and operation of their systems and facilities, to reduce the risk to people, to an acceptable recognized in country level.
Under the UK Health & Safety Regulations, it is vitally important that any organization designing, building, testing and installing components or systems for safety related applications, must have in place, corporate policies and functional safety management procedures to ensure the integrity and provenance of the product.
The policies shall outline the company directors commitment to safety and the procedures shall provide qualitative defenses against systematic failure (human error) within the organization.
The UK regulations came about, following several major accidents such as Seveso Italy and Flixborough in the UK. The EU and UK regulations developed through the Seveso Directives and in the Control of Industrial Major Accidents Hazards(CIMAH) regulations, the latter developing into the Control of Major Accident (COMAH) regulations.
Although the regulations identified the need to control hazards, they do not specify how to quantify risk for activities or how to manage safety related system design, build and test.
Due to the introduction of more and more software in safety related systems and following guidance published by the HSE in the late 1980's, the International Electrotechnical Commission (IEC) began work on international safety, which led to the development and release of IEC 61508; Functional Safety of Electrical/Electronic/Programmable Electronic Safety - Related Systems.
Although the reduction of risk is a legal requirement, the IEC 61508 standard is voluntary, rather than written in law. However, as it provides an excellent framework to work within, when demonstrating compliance, it is seen, along with other standards, as a good basis for company procedures and policies.
Any company adopting this standard, or IEC 61511, which is based on IEC 61508 and specifically developed for the process industry, will be seen to demonstrate Functional Safety Capability (FSC) throughout the lifecycle of their product or system.
Company FSC is an integral part of their ISO 9000 QA Procedures and here at Whorlton , we can help to develop and write your procedures, with supporting documentation, or fill any gaps within your existing systems, necessary to meet the intent of the IEC standards.
At Whorlton , we can also produce project specific documentation in line with your existing functional safety procedures, provide verification services, or even manage validation testing such as at the factory or on site during Factory Acceptance Testing (FAT) and Site Acceptance Testing (SAT).
Whorltons expertise, from practical ‘hands on' industrial experience, covers the whole system lifecycle, from the initial hazard identification exercises through design, build, test, install, and commission, including decommissioning.
Typically, we can produce your project Functional Safety Management Plan (FSMP) and Verification & Validation Plans (VVP), with continuous or periodic support as and when required.
If you would like more information on how Whorlton can help your company with Functional Safety Regulations - Policies and Procedures please contact us.
Other Services
Functional Safety Audits and AssessmentsHAZOP
Risk Reduction Targets
Design
Verification and Validation
Commissioning and Operation
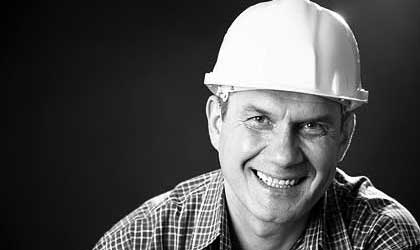
Latest Case Study
Chemical Facility - Hardwired Safety Instrumented System (SIS) Upgrade
This was an extremely interesting and challenging project, involving detailed planning, site surveys, design, build, test, commissioning, with close liaison with operations on a live facility, with limited process shutdown windows.
Read more