Chemical Facility Hardwired Safety Instrumented System SIS Upgrade
Wednesday, March 4, 2015
This was an extremely interesting and challenging project, involving detailed planning, site surveys, design, build, test, commissioning, with close liaison with operations on a live facility, with limited process shutdown windows.
The customers existing Emergency Shutdown (ESD) system, had come under the scrutiny of the regulator, due to its lack of independence from the process control system and its fragmented design, with respect to shutdown hardware locations, which caused access difficulties for maintenance across the site in several locations.
The original system comprised some 100 hardwired safety loops, connected at various locations across the site. The project scope was to build a relay logic based shutdown system in two field mounted panels, which could tie into field sensors and final elements, but be independent of the control system.
In some cases, existing field final elements were used and for other applications, additional valves were installed to achieve the necessary independence between control and safety.
The client required SIL 1 capability for the new system, based on their Process Hazard & Risk Analysis (PHRA) work. The client also wanted the system designed in accordance with IEC 61511.
The first phase of the project involved an exhaustive survey of the existing shutdown facility, comparing it with the clients shutdown logic and new logic developed during the PHRA.
It was vitally important that every shutdown loop was located and its function agreed with the client.
To ensure no surprises at the tie-in stage, each loop was identified by working closely with the clients maintenance and operations departments. Following trip loop identification, to establish loop function, temporary break-in investigations of loops were conducted, during short shutdowns or when batch process conditions allowed.This process also identified when additional interface hardware was required, to tie-in seamlessly to existing shutdown loops.
This survey established the basis of design and what level of planning and detail was necessary to physically install and test the system on the live facility.
We produced the Project Safety Requirement Speciation (SRS), Project Management Safety Plans, detailing all roles and responsibilities, supported by Installation Plans/Work Packs and Verification and Validation Plans. Everything had to be detailed and slotted into a program of works, due to it not only being safety related in accordance with IEC 61511, but the installation was taking place in a working facility.
Once the panel design had been completed and rigoursly tested in the factory, the panels where shipped to site, installed and cabled up ready for the tie-ins.
So as to manage the tie-ins and have a measure of the install progress at any time of the build, we produced Work Packs for each loop, which contained detailed installation and test procedures for the technicians. The Work Packs also included the name and signature of the technician, who had carried out the tie-in works, for traceability and system provenance.
The installation was in two phases, install up to the point of tie-in, then break in during the shutdown or when the batch process allowed.
The final tie-in took place over a weekend and was completed on time, without any disruption to operations.
This project could of caused major loss of production issues for the client, but because of our detailed plans and close co-operation with maintenance and operations at every stage of design, install and testing, it all went according to plan with no process downtime.
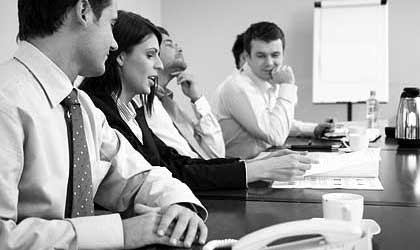
What We Do
We offer a full range of functional safety services, including Functional Safety Regulations, Functional Safety Audits and Assessments, HAZOP, Risk Reduction Targets, Design, Verification and Validation, Commissioning and Operation, and more.
Services we offer